Two researchers from the Whiting School of Engineering’s Department of Chemical and Biomolecular Engineering have teamed up with colleagues at The University of Alabama and Oak Ridge National Laboratory to spearhead a project aimed at demonstrating the commercial readiness of an innovative method of creating jet fuel from plants, helping the airline industry meet goals for using a renewable fuel source and reducing greenhouse gas emissions.
Supported by $2.5 million from the United States Department of Energy, the team is developing a catalyst that can chemically convert ethanol into butene, which can be further refined into aviation fuel identical to the current crude oil-derived variety. This sustainable aviation fuel (SAF) has the potential to offset a plane’s emissions of harmful carbon dioxide, or CO2, thanks to the CO2-absorbing plants used in its production.
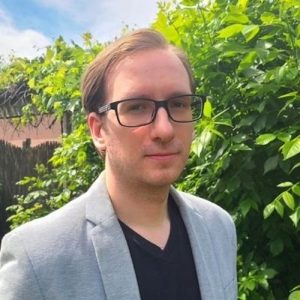
Brandon Bukowski
“We can electrify cars—but electrifying an airplane is difficult,” said Hopkins team leader Brandon Bukowski, assistant professor of chemical and biomolecular engineering at Hopkins. “Battery weight contributes significantly to the total weight of electric cars, but planes have strict weight limits; they need to be as light as possible.”
Bukowski predicts that batteries will eventually become light enough to be used in aviation, but until then it is imperative to find a more environmentally healthy way to power aircraft. He is using atomistic modeling—a method that simulates how a substance’s atoms respond to stimulus—and machine learning, together with experimental catalyst synthesis, performed in the lab of Bloomberg Distinguished Professor Michael Tsapatsis, to assess how the catalysts formulated by University of Alabama researchers will perform under realistic conditions.
“The problem we are trying to solve is something you cannot test easily in the laboratory,” Bukowski said. “This is something that needs simulations and modeling to get to that next level.”
Experts say that SAF has the potential to deliver the same performance as petroleum-based jet fuel, but with a fraction of its carbon footprint, and can be made from renewable biomass and other resources such as corn grain, algae, agricultural and forestry residues, and municipal solid waste streams. The federal government estimates enough biomass can be collected sustainably each year in the U.S. to produce 50-60 billion gallons of low-carbon fuels.
The Hopkins team is closely examining a crucial factor: catalyst deactivation, which occurs when the catalyst gradually loses productivity over time, rendering the cost-to-benefit ratio no longer feasible.
“If we can get a higher yield and make a better product with a stable catalyst, then companies will be interested,” Bukowski said. “Corporations don’t want to see a light bulb light up once; they want to see it light up the 500th time. By combining simulations with precise catalyst synthesis from the Tsapatsis lab, we can make meaningful advances in designing a stable catalyst.”
Because aircraft must operate at different altitudes and temperatures, and require a large amount of energy for takeoff, any new SAF must match the chemical formulation of the petroleum-based fuel currently in use. Modifying existing planes and future aircraft design and manufacturing to accommodate fuels distinct from existing petroleum-based jet fuel would also be prohibitively expensive and difficult, the researchers say. The team is working to prove that their method is repeatable and sustainable in the long run.
“The model can tell you whatever you want, but you need to ground it,” Bukowski said. “Hopkins, especially with The Ralph O’Connor Sustainable Energy Institute has a really good team to do that.
This story was written by Jonathan Deutschman and Adam Jones, and was originally featured in the Hub.