This is a portion of a story that was written by Andrew Myers. The full version can be read in the JHU Engineering Magazine.
Inside the historic Stieff Silver Building, Johns Hopkins has built the world’s top facility for studying the atomic structures of materials. Researchers across the Whiting School are using it to reshape fields from energy to oncology.
The alligator gar is not an attractive fish. It boasts a long, toothy snout that looks like a cross between a duck’s bill and an alligator’s grin, by which it earned its name. It can grow to well over six feet and weigh upward of 300 pounds. The alligator gar is a formidable predator, too, but being an apex predator does not mean it lacks natural enemies. And that notion raises the question of why such an ungainly species has survived, virtually unchanged, for nearly 200 million years.
That endurance, say evolutionary biologists, is likely due to the alligator gar’s remarkable spade-like scales. They are just plain tough. It was that toughness that brought the Army Corps of Engineers to Ken Livi, a research scientist and director of operations at Johns Hopkins’ Materials Characterization and Processing (MCP) facility.
The Corps came calling, hoping he might use the array of world-class imaging tools at Johns Hopkins to reverse engineer why those gar scales are so durable and to possibly turn that knowledge into better armor and shielding, like those that protect spacecraft on reentry.
TOOLS OF THE TRADE
The tools of Livi’s world—electron microscopes, spectroscopy, X-ray computed tomography, and others—would allow his team to peer into the very atomic structure of the alligator gar’s scales. In all, Livi used no fewer than eight imaging and analysis technologies to examine the scales.
In the end, the team confirmed that the scales comprise an outer layer of ganoine, a hard material akin to tooth enamel, sitting atop a porous-yet-flexible bone-like material. Critically, Livi and team discovered that the two layers are not fused or otherwise glued together, but bound by “rasps” of hydroxyapatite (HAp) extending from the underside of the enamel into the bony structure below. What’s more, those rasps are angled toward the outer edge of the scale to create anchoring points, like tent stakes, locking them in place and preventing the material from fracturing into layers, or delaminating, and distributing load when compressed by, say, a predator’s bite.
“What makes this material so fascinating is that every part of this simple scale is exquisitely engineered for a purpose,” Livi explains. “The rasps angle in and keep the enamel from popping out. Even the arrangement of collagen changes depending upon its location. We couldn’t have learned any of this without tools like those at the MCP facility.”
NOT YOUR MOM’S MATERIALS CENTER
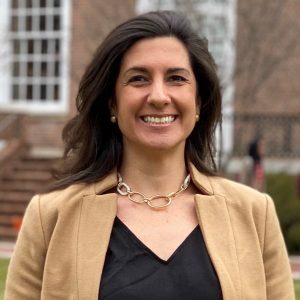
Mitra Taheri
Such is precisely why, not long after Livi’s research was published in 2016, Johns Hopkins began to invest aggressively in the Materials Characterization and Processing facility, putting more than $25 million into this state-of-the-art lab, classroom, and office space. The MCP today boasts a collection of processing and characterization equipment that is, in its entirety, is considered unmatched in the world.
“This may seem like your ‘mom’s materials center,’ but it’s not at all,” says Mitra Taheri, a professor of materials science and engineering at the Whiting School and director of the Materials Characterization and Processing facility.
“It’s really something built for the next several decades of science,” says Taheri, who also heads the Whiting School’s Dynamic Characterization Group, serves as a Faculty Fellow of the Hopkins Extreme Materials Institute, and is a core researcher for the Ralph O’Connor Sustainable Energy Institute (ROSEI). “The MCP is a development lab where we’re working with microscope and processing manufacturers to remake these tools with embedded artificial intelligence and computing toolsets to be ‘thinking machines’ for processing autonomy. We’re both synthesizing new materials and helping create new tools to produce [those materials].”
The facility is overseen by the School of Engineering, but available to any researchers at Johns Hopkins as well as corporate and government clients eager to lease time on its cutting-edge machinery. All have a vested interest in peering deeper into materials than ever before and creating bespoke materials for next-generation applications. The MCP makes that possible as never before.
THE ‘ZERO’ ENVIRONMENT
The next room includes the first piece of equipment in the facility to resemble a traditional microscope, albeit at tabletop scale—an entire tabletop, that is. What would traditionally be an eyepiece plays host to a digital camera transmitting imagery to an observation room nearby. This is what is known as a focused ion beam-scanning electron microscope, a FIB-SEM. It operates on the same principle as a traditional light microscope, Taheri says, but employs a beam of ions to slice into a sample in ultrathin layers while a column of electrons illuminates each cross-section for high-resolution imaging.
Electron microscopes, like the transmission electron microscope (TEM) in the next room along the hall, have an electron beam that is far more sensitive than any light-based microscope, Taheri says, but are also much more “finicky.” With a TEM, the slightest vibration (a footstep or the slightest sound) can imperil results.
“We need a zero environment—no vibrations, no interference. With some of these more sensitive transmission electron microscopes, the samples are so small a single breath—‘huh,’ just like that—and it’s curtains,” Taheri says, making a slight puff for dramatic effect.
A key decision in creating a zero environment was Johns Hopkins’ choice to forego a new building and instead renovate the Stieff Silver Building at the southwest corner of campus. While the building’s legacy as a precious metal foundry provided a metaphorical hook—Taheri refers to the facility as “transforming the modern foundry”— something more was at play. The Stieff building rests directly on bedrock, an unmatched foundation for the MCP’s ultrasensitive machines.
All rooms are individually isolated to further dampen vibration. Inside, the rooms look more like recording studios than labs. The hospital-white walls are canted slightly so as not to meet at right angles, and each is peppered with odd-angled acoustic panels to further deaden sound. Many rooms are fitted with large cooling panels that hold temperatures within tight specifications to eliminate thermal expansion and contraction that can likewise imperil results. Last but certainly not least, the most sensitive electron microscopes are also prone to electromagnetic disruption and must be shrouded in room-within-a-room metal superstructures that jam interference.
Click here to read the rest of the story.