A team of Johns Hopkins researchers affiliated with the Whiting School of Engineering’s Ralph O’Connor Sustainable Energy Institute (ROSEI) is developing a new, more sustainable, and decentralized way to produce ammonia fertilizer using specially engineered organisms and electrochemistry.
“Current methods used to create ammonia, invented more than a century ago, are energy-intensive and emit a lot of carbon dioxide,” said Ruggero Rossi, an assistant professor of environmental health and engineering and one of the project’s leaders. “We’re trying to eliminate the need for large-scale ammonia manufacturing plants and, by empowering ammonia production at a local level, eliminate the expense and environmental cost of shipping it from factories around the world. What’s more, our approach would be powered by renewable energy without any carbon dioxide being sent into the atmosphere.”
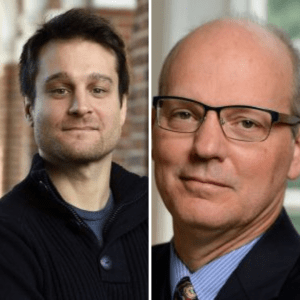
Ruggero Rossi and Mike Betenbaugh
The innovative process being designed by Rossi and Michael Betenbaugh, a professor of chemical and biomolecular engineering, partners elements of electrochemistry and microbes—specifically Rhodopseudomonas palustris cells—that create ammonia. The goal is to manipulate the cells to maximize the amount of ammonia they create, capture the CO2 the cells emit, and then funnel it back into the microbes for use as food.
“Our system is a loop: The microbes create ammonia and emit carbon dioxide, which is then transformed back into food for the microbes. What I like most about our approach is that every farmer could have their device sitting in a barn next to a field, making their ammonia from renewable energy. Achieving that would be world-changing,” said Rossi.
The researchers’ method uses engineered microbes as catalysts to convert nitrogen gas into ammonia. They do this in electrochemical cell, applying electricity to control the microbial metabolism and boost ammonia productivity. In this process, one part of the cell produces the ammonia and the other parts converts carbon dioxide into a biodegradable chemical that can be recycled.
This work is supported through a two-year, $500,000 National Science Foundation Future Manufacturing grant.